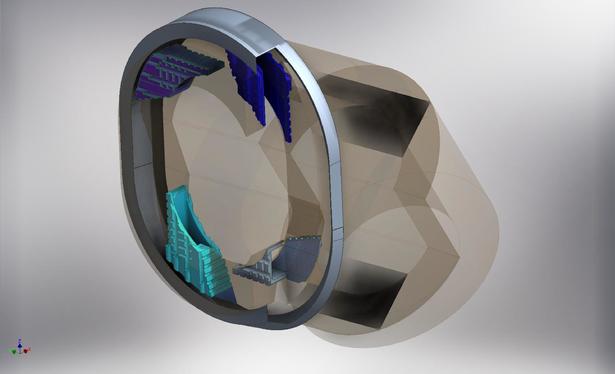
ALSTOM s.r.o. – DENOX, Prunéřov II
DITHERM replaced the previously used steel nozzles with for ceramic nozzles. They have a higher shape stability and resistance to temperature changes than the original nozzles. Among other things, they are more environmentally friendly. Thanks to this, DITHERM has increased the life of the nozzles and, in particular, reduced the extent of repair of the lining around the nozzles.
2012 – design and implementation. Cooperation continues to this day.
ČEZ Power station, Hodonín
Increasing the lifetime of boilers - DITHERM carried out a complete replacement of the bottom of the combustion chamber, including the steel structure and the recovery of the properties of the jet bottom; we also ensure replacement of combustion chambers, cyclones, exhaust ducts, ducts and siphons, ash coolers; among other things, we have worked out complete design documentation and designed and supplied refractory materials. The lining of these aggregates had to be 100 % resistant for biomass. This creates a strongly alkaline environment that is not good for the lining. Special materials have been developed in co-operation with the manufacturer to obtain the target level of resilience. Among other things, DITHERM has been able to dismantle and clean the bottom of the combustion chamber with a very high hardness. In 2012–2013.
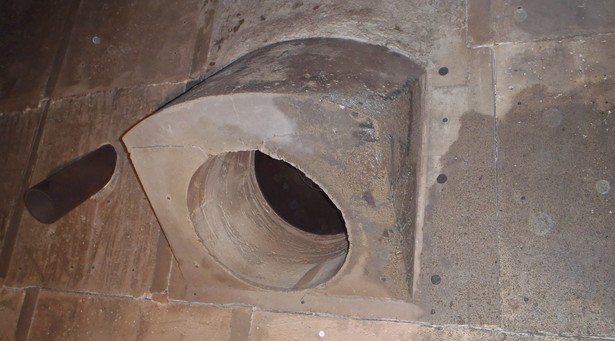
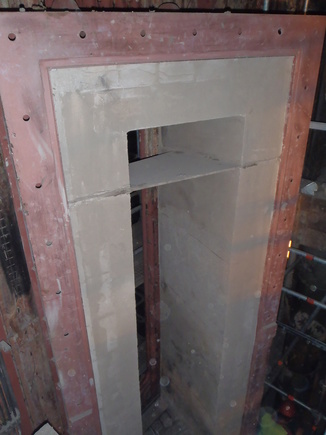
ČEZ Power station, Mělník
Project to reduce emissions during boiler operation; DITHERM has provided the complete assembly of a semi-rigid liner for OFA, AGA and SNCR tube deflections, as well as dismantling and mounting of semi-hard linings for burners. Chemically bonded materials were used to accelerate the aggregate uptake (without final drying). During the project, there were major design changes that DITHERM was able to adapt in a short time, both in the organization of work and its quality. In 2014–2015
KOFING, a.s. – Increasing the life of the ceramic lining
Increasing the lifetime of the ceramic lining of the boiler 100 t/h in the front wall area, ArcelorMittal Ostrava a.s.
DITHERM replaced the original burner nozzles with composite nozzles made of steel and ceramics. We have altered the composition of the burner wall both in design and composition of materials. This has greatly reduced the cost of maintaining and repairing this part of the boiler, as the burner walls belonged among the most frequently repaired parts of the aggregate.
2014 – design and implementation.
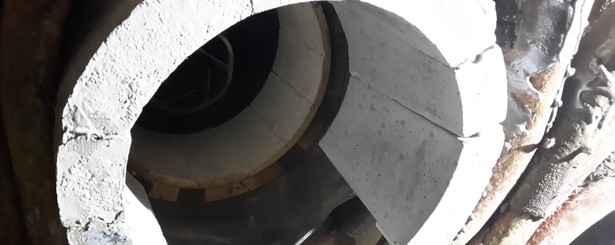
Kronospan ČR
General overhaul of the ceiling of the DTD combustion chamber; DITHERM supplied dismantling of ceiling lining, materials including fixings, and ceiling linings. The DITHERM project was realized in just 8 days. In 2015
Mondi Štětí
General repair of the fluid boiler 220 t/h - DITHERM completely replaced the cyclone linings in the part of the chamber, parts of the bottom and walls of the combustion chamber, and the burners. DITHERM shortened the implementation deadline to 12 days! From 2011 to 2015
Opatovice Power station
Nox Reduction Project; DITHERM has provided the complete design documentation, selection and delivery of materials, as well as dismantling and assembly of linings and insulation of boilers. DITHERM has carried out very good work here, both in the selection of materials and during assembly and its organization. The assembly team was able to respond to unplanned changes in a short time, and maintain the quality and performance of the work. Gradually, we shortened the implementation time. In 2014–2016